Why a Direct Drive Motor Could Be the Smartest Upgrade for Your Motion System…
When designing high-performance motion systems, engineers are constantly faced with the challenge of improving precision, efficiency, and reliability, all within compact, often constrained environments. One solution continues to gain traction across industries like automation, robotics, and medical technology.
In this blog, we’ll explore what a direct drive motor is, why it outperforms traditional systems, and how integrating one particularly through Franke’s own solutions, can elevate your project from adequate to exceptional. If you already know a direct drive is the best fit, reach out and contact us today…
What Is a Direct Drive Motor?
It is a type of electric motor that eliminates the need for mechanical transmission elements such as gearboxes, belts, or pulleys. Instead, the motor is connected directly to the driven load. This design significantly reduces friction, backlash, and wear offering smoother, more accurate motion control.
Unlike conventional servo systems, direct drive motors deliver torque and rotation directly to the application, resulting in faster response times, increased positioning accuracy, and lower maintenance requirements.
Key Advantages of Using a Direct Drive Motor
- Precision and Responsiveness
The absence of mechanical linkages means minimal backlash and superior positioning accuracy, a critical benefit in applications such as robotics, CNC systems, or optical inspection. - Compact Design
With fewer moving parts, direct drive motors often have a smaller footprint, ideal for integration into compact systems where space is at a premium. - Reduced Maintenance
Without belts or gears to wear out, systems powered by direct drive motors experience less downtime and require fewer part replacements. - Energy Efficiency
More efficient power transfer results in lower energy consumption, making direct drive motors an eco-friendly choice for continuous operation systems. - Quiet Operation
The streamlined mechanism of a direct drive motor produces significantly less noise, a key advantage in medical and laboratory environments
Real-World Applications of Direct Drive Motors:
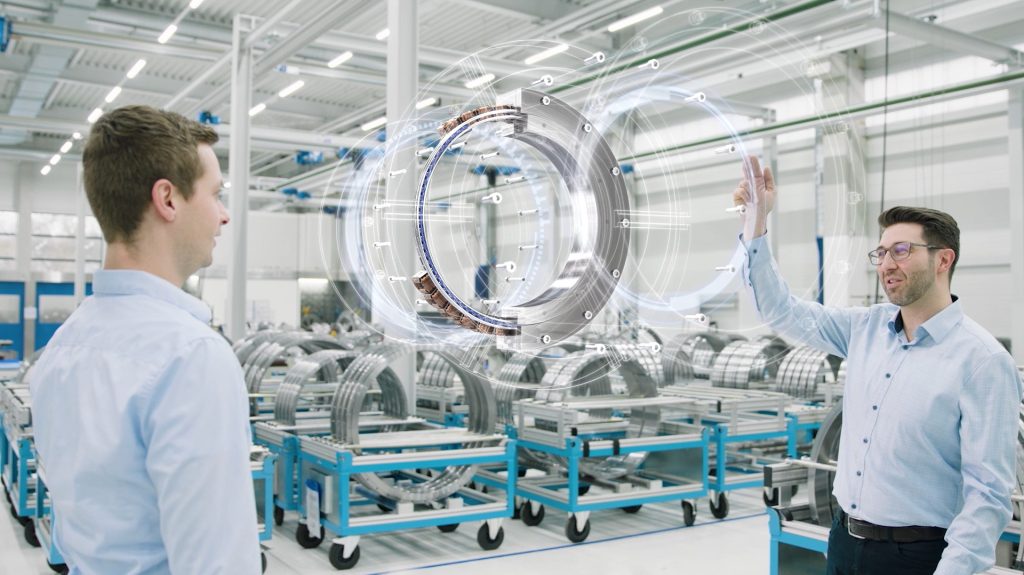
Direct drive motors are becoming a go-to solution in industries where precision and reliability are non-negotiable. These include:
- Robotic arms used in manufacturing and assembly
- Rotary tables for metrology and machining
- Medical scanners and lab automation equipment
- Semiconductor processing and packaging systems
Whether it’s high-speed positioning or ultra-smooth rotation, the direct drive motor is proving essential in pushing innovation forward.
Franke FDB: A Smarter Solution
At Franke UK, we take the direct drive concept one step further. Our Franke Direct Drive Bearings (FDB) integrate the motor directly into the bearing unit, combining compact form with high dynamic performance.
The result? A ready-to-integrate motion system that reduces complexity, saves space, and enhances machine responsiveness, all without compromising on reliability. With decades of expertise in wire race bearing technology, we’ve created a solution that meets the demands of today’s cutting-edge automation environments.
Is a Direct Drive Motor Right for Your Project?
If your application demands faster movement, reduced wear, and precision performance, the answer is likely yes. Switching to a direct drive motor can simplify your mechanical design while boosting long-term performance and ROI.
To learn more about how Franke’s direct drive solutions can be tailored to your system, visit our FDB product page or get in touch with our engineering team.